The Doctor is Inside your Body
Posted on: in Blog
Ilika’s battery technology is enabling true mm-scale IoT implantable medical devices
Recent advances in thin film solid state energy storage devices are enabling exciting new applications. Such batteries are created using semiconductor production techniques where cathodes, electrolytes and anodes of 10’s of μm thickness are deposited onto a carrier layer, in Ilika’s case a 6” wafer. Thinning and dicing the wafer results in discrete cells, about 150 μm thick, which can be stacked to form batteries. A 0.06 CC volume battery can store about 1 mAh.
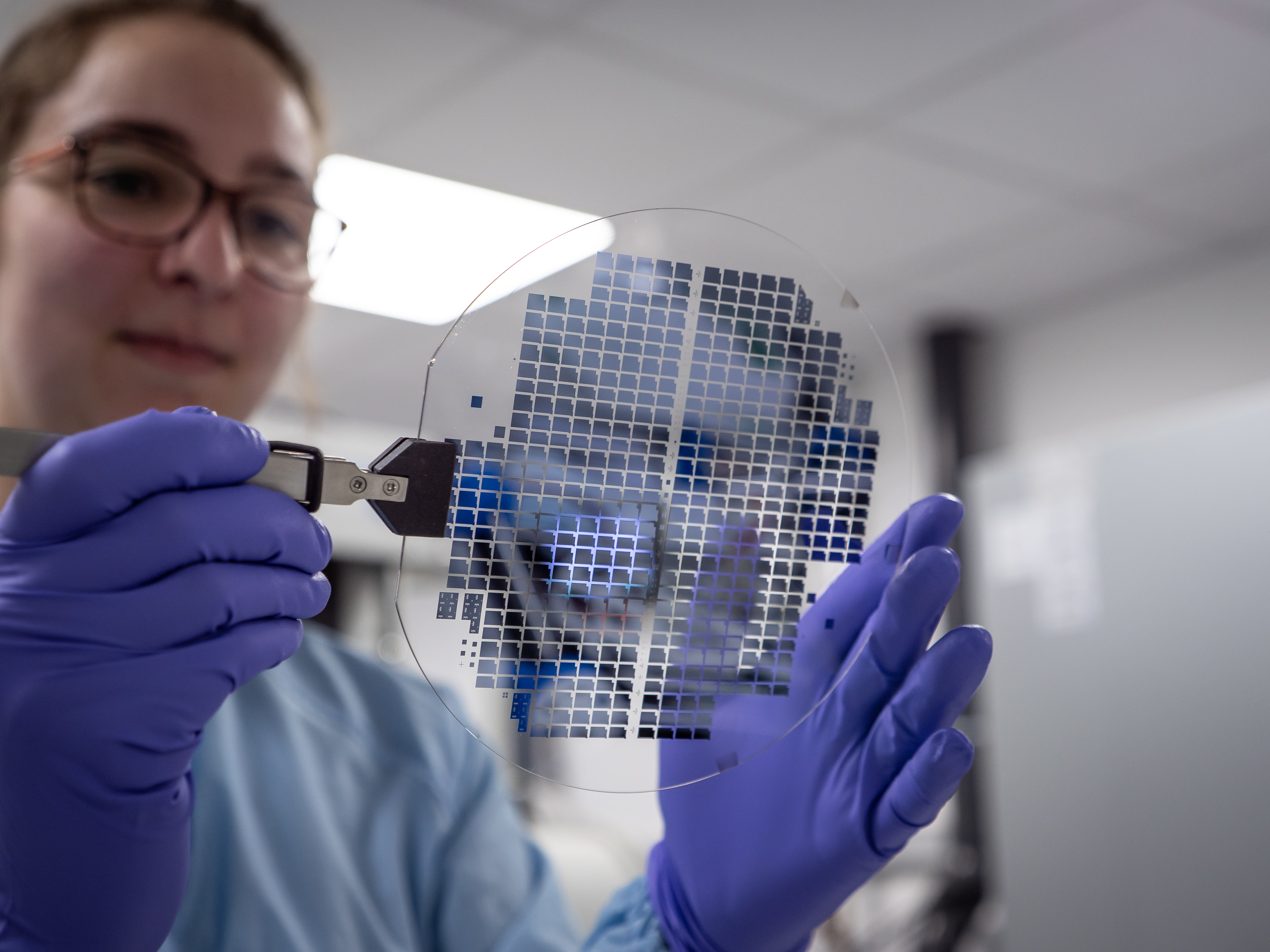
Previously, the production of thin film batteries on expensive and sophisticated equipment placed the technology into a high value, but low volume, industrial category. Today’s applications are based around the high temperature capability (to 150°C), or the sub 1mm thickness of the thin film battery. Thin film solid state technology also supports high charge and discharge rates (C=>10) allowing a 0.3 mA battery to drive the transmit and receive signals on a Bluetooth radio device and so be part of an industrial sensing solution. If coupled with an energy harvester this opens the door to remote condition monitoring over long time periods, taking advantage of the technology’s high cycle count.
Addressing a number of critical factors is enabling thin film solid state batteries to move into the mainstream of battery applications. These include use cases requiring 10s of thousands of devices able to absorb a high initial price point, development of devices with higher energy densities, the deployment of high capacity and high accuracy manufacturing equipment and, for the medical sector, publishing long term reliability test data.
The technology has so far been developed by SMEs or research-focussed technology centres, both lacking either the strategic intent or access to capital to move the technology into the medical arena. Ilika is a listed company (UK LSE-AIM) supported by institutions and investors proven over the years to take the long-term strategic viewpoint. By 2020, our analysis showed us that the time had come to invest across all the critical factor areas with a view to becoming a volume manufacturer of thin film solid state batteries. The investment was secured and equipment orders placed as discussed later in this piece.
Sitting alongside this new technology are important breakthroughs in low energy ultrasonic radio, in-body-battery charging and energy harvesting which will influence designers. A new generation of medical start-ups is emerging, perhaps best described under the banner of Cyber-Physical Human Systems. In layman’s terms, an interconnected array of sensing and therapy delivering devices created at mm-scale and placed around the body, much nearer to the point of therapy delivery, capable of staying in the body for many years.
Applications
In our video Miniaturisation of Next-Generation Implantable Neuromodulation Devices to Tackle the Opioid Crisis, we discuss advances and challenges of these innovative applications and how they can help tackle the opioid crisis where over-prescribed painkillers are leading to addictions and many deaths. An alternative therapy, via implanted devices sending a blocking signal to the nerve, exists today but deployment has been limited due to the current size of these devices. Smaller implants requiring simpler surgical procedures are seen as critical. Research also continues to uncover a wider array of therapies based around the stimulation of nerves aimed at seizures, sleep apnoea and migraines amongst many examples.
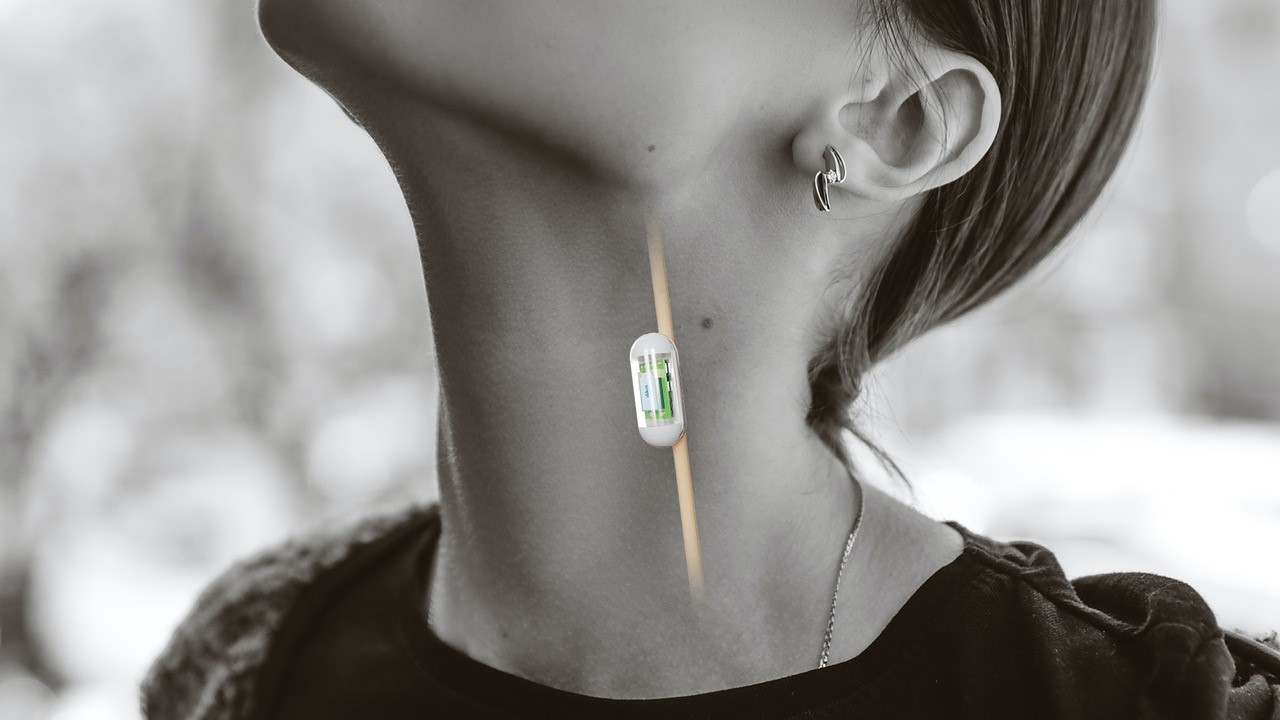
Communication-enabled sensing applications include blood pressure, heart rhythm and glaucoma as well as a host of medical conditions that are crying out for smaller, less obtrusive and easier to install solutions. In the field of orthopaedics, such as a hip or knee implants, real time data on patient adherence to physio routines will be a great aid to better outcomes.
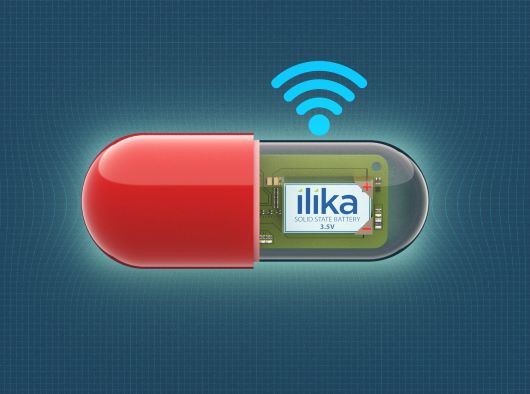
Whilst for the above applications a mm-scale energy storage device allows a significant improvement in device design, there are some applications that are enabled for the first time with ultra-thin mm-scale battery technology. There are at least ten companies around the world, some very well known, who are working on smart contact lens products with either a medical or an AR/VR focus. Furthermore, continuous improvements to the performance of solid state batteries may open up applications in implanted hearables and smart wearables such as smart dental braces.
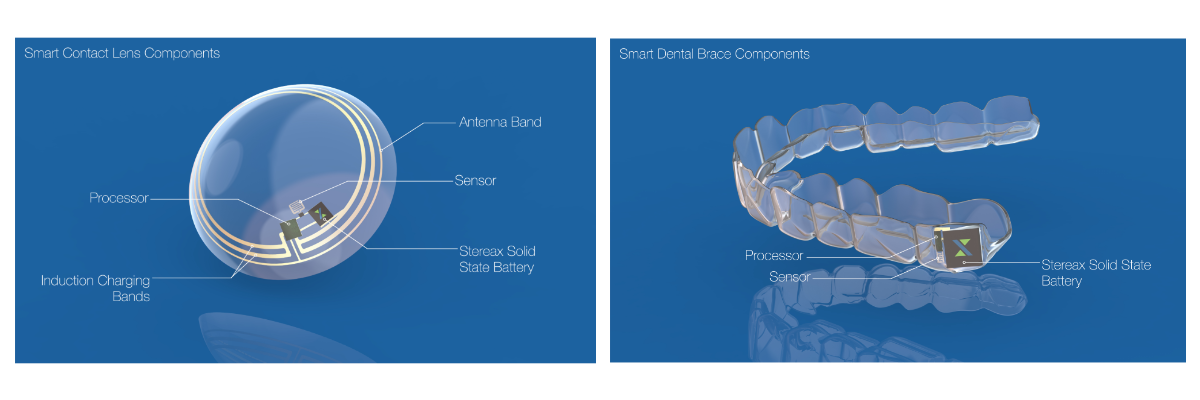
The Technology
The production of a Stereax solid state, thin-film battery takes place on a glass 6” wafer, used as a non-functional substrate layer. Initial depositions are of the 1stcurrent collector (sputtered) and then the cathode, via thermal evaporation. The thickness of this layer will determine the amount of lithium available for transport and so capacity of the battery. Next, electrolyte, anode, second current collector and primary encapsulation (insulation) layers are deposited. Following the addition of a secondary encapsulant the completed wafers are quality tested and passed to a set of thin and dice processes, here the substrate layer is thinned to below 100 μm and the individual batteries diced from the wafer. At this stage we have a battery cell 150 μm thick which can be used alone as an ultra-thin battery, or it can be stacked to make higher capacity devices as shown in the picture. Development work on the deposition and thinning processes over the next year is set to take energy densities of the resulting battery beyond 200 Wh/L.
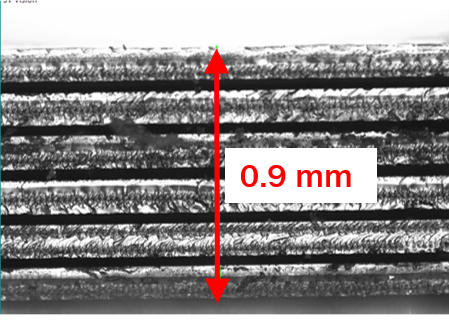
Future Outlook
There remains a lot to be done at Ilika, for our customers, and in the other supporting technologies. Novel therapeutic devices can take 3-5 years to reach market at a cost of $10’s millions but the benefits to us all as individuals, and in cost savings to insurance and health services are great. At Ilika, we’re already working closely with companies to support their product design with customised batteries that will enable their device to reach its full potential, and low volume prototype. Whilst novel active implanted medical devices can take some years to reach market, we’re already working with companies offering dedicated battery design programs and low volume prototyping. If you’re developing a next generation implantable device, contact us now to find out more about how we can help info@ilika.com