Ilika Technologies - From 2004 to 2024
Posted on: in Blog
Ilika Technologies has turned 20 years old. For those of you who haven’t followed the company since the early years, this is a short history of Ilika. Guided by three consecutive chairmen over the years, this is a story in three parts, taking Ilika from start-up to the mature company it is now.
The High-Throughput Years (2004-2015)
Some of you might be surprised to learn that Ilika did not start as a solid state battery company. Ilika means “materials” in Greek and this is where the story starts: the company was formed when CEO Graeme Purdy took charge of a start-up from the University of Southampton, UK, aiming to commercialise the technology developed in the Department of Chemistry by Professor Brian Hayden and co-founder, then postdoc, Dr Samuel Guerin. Professor Hayden, who became Ilika CSO, had designed a machine that could rapidly make and test hundreds of systematically-varying materials in minutes. This so-called “combinatorial” approach, very common in the medical drug industry and now adapted for other applications, could very quickly discover new materials or optimize the properties of known materials by way of “doping” (i.e. very slightly modifying their chemical composition). This was a very attractive offer to companies all over the world, who realized that Ilika could help them accelerate their product development, with Ilika essentially becoming their materials discovery R&D arm. Over these early years we worked on optimizing fuel cell catalysts, hydrogen storage materials, phase change memory materials and, crucially for Ilika’s future, with Toyota on solid state battery materials. When Toyota come to us in 2008, wanting to develop new battery materials that would replace the NiMH battery in their early Prius, they knew that lithium-ion batteries were the future of batteries in transportation but were concerned with the well-publicised, although rare, possible fires with lithium-ion. Solid state was going to be the long term, safe future of batteries.
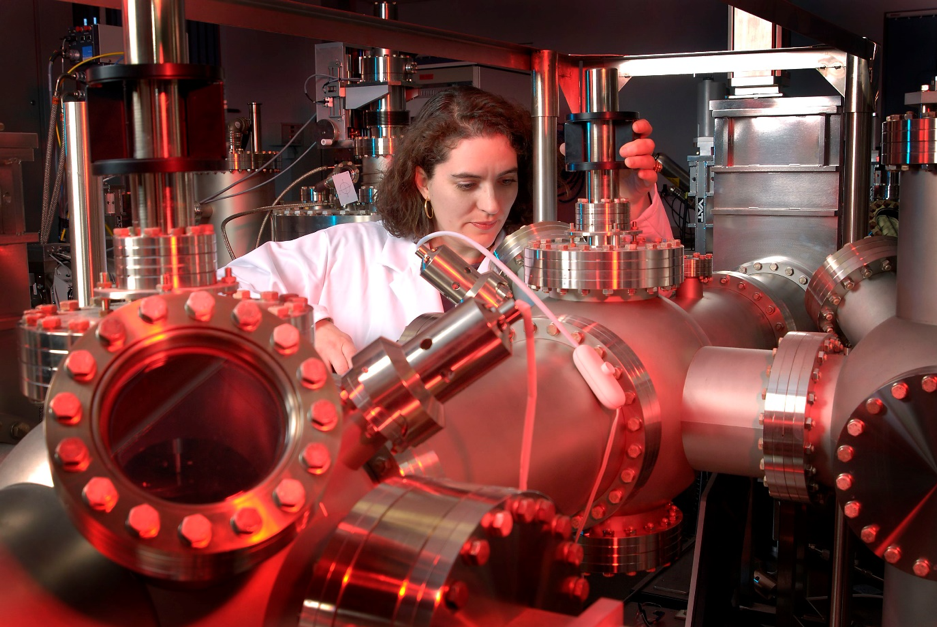
During this period, senior management and chairman Jack Boyer knew that Ilika’s “contract R&D” business model, although bringing in regular revenues, was not conducive to growth. In-house materials R&D programs were developed, for the purpose of building Ilika’s own IP portfolio and know-how in a few selected, materials classes. We would then commercialise the most attractive discoveries through product development and manufacturing programs.
The Stereax Years (2015-now)
Now with chairman Mike Inglis on board, the business model was refined, and the second phase of Ilika’s life started. Prior to joining Ilika, Mike was a senior executive at ARM, the British semiconductor and software design company based in Cambridge. Ilika would follow ARM’s licensing model, adapting it to batteries: we would design new solid state battery (SSB) concepts, develop a road map of market-driven products, exemplify volume-manufacturing at pilot level, and license the technology to companies excited to take the technology, manufacture it at volume and commercialise in their favoured markets.
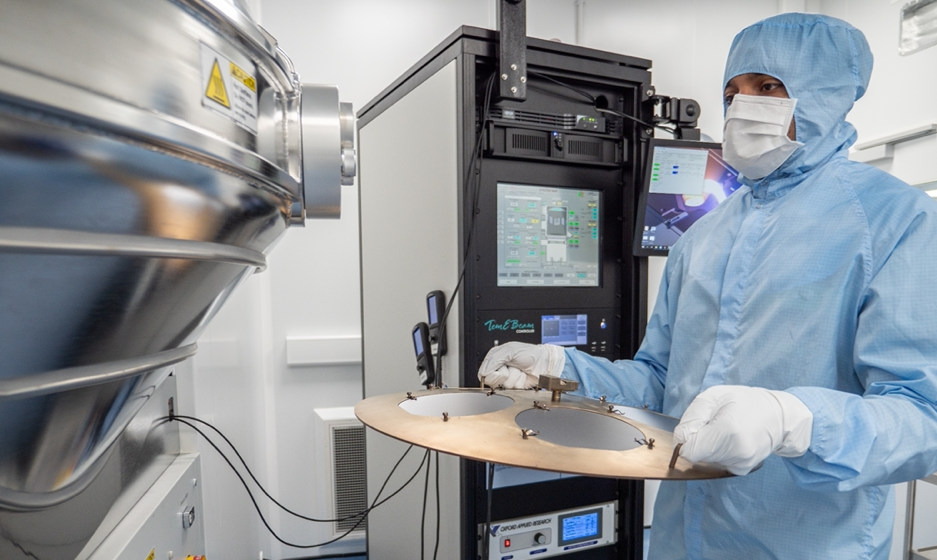
“Stereax® ”, our first SSB product family, was born. Early market research concluded that various markets were in need of new battery technologies: the world of electronics (microcontrollers, sensors, communications…) was (and still is) miniaturizing; the “Trillion-sensor” Internet of Things was going to revolutionise connections between people, machines and services; medicine was hitting a dead end with using prescription drugs to solve all conditions: the USA opioid crisis proved this, and electroceuticals (small electronic medical devices) were going to take over. The only problem was that the batteries were not keeping up with this miniaturisation trend.
This is why we developed Stereax, our mm-scale battery. To make this happen, we had to adapt the equipment designed by Prof Hayden: first, in 2014-15, we built a larger, faster, more robust R&D production tool at the University of Southampton. Our Stereax road map had started. Then, in 2020, we built our own pilot line: this was made particularly difficult when the COVID 19 pandemic kicked in! At the end of 2021, we opened “Discovery House” and started producing small volumes of battery cells on equipment that is representative of volume manufacturing. In this period, it became clear that Stereax’s early market entry point was going to be MedTech. We had attracted interest from a healthy portfolio of companies and product designers who were waiting for a minuscule battery to build next-generation medical implanted devices in fields such as: neurostimulation (treating conditions such as Alzheimer’s, Parkinson’s, chronic pain…), smart orthopedics (making prosthetic joints smart to make sure implantation was successful), cardiac sensors, and outside the body into smart dental braces (monitoring tooth decay) or ophthalmic (monitoring glucose level in diabetic people).
In 2023, Cirtec Medical, the US-based vertically-integrated outsource partner for medical devices and components, and Ilika agreed to a 10-year license contract to industrialise and commercialise Stereax in MedTech markets. At the time of writing this blog, Cirtec are commissioning the production equipment with first batteries available from the line in 2025.
The Goliath Years (2018-now)
For many years, people were asking us if we could scale Stereax up in order to develop solid state batteries for Electric Vehicles. However, the Stereax semiconductor process was never going to be rapid enough and cost efficient to be adopted for EV batteries. Despite this, we had gained invaluable expertise in solid state materials and processes, particularly in solid electrolytes and silicon anodes. The seed was planted for the idea of commencing a second SSB program and new chairman Keith Jackson was now on-board: we were fortunate and grateful when we attracted support and funding from our investors and UK government grants. We started 3 R&D programs in 2018, collaborating with JLR, McLaren and Honda, which led to chemistry-selection and a definition of our goals in terms of products and markets.
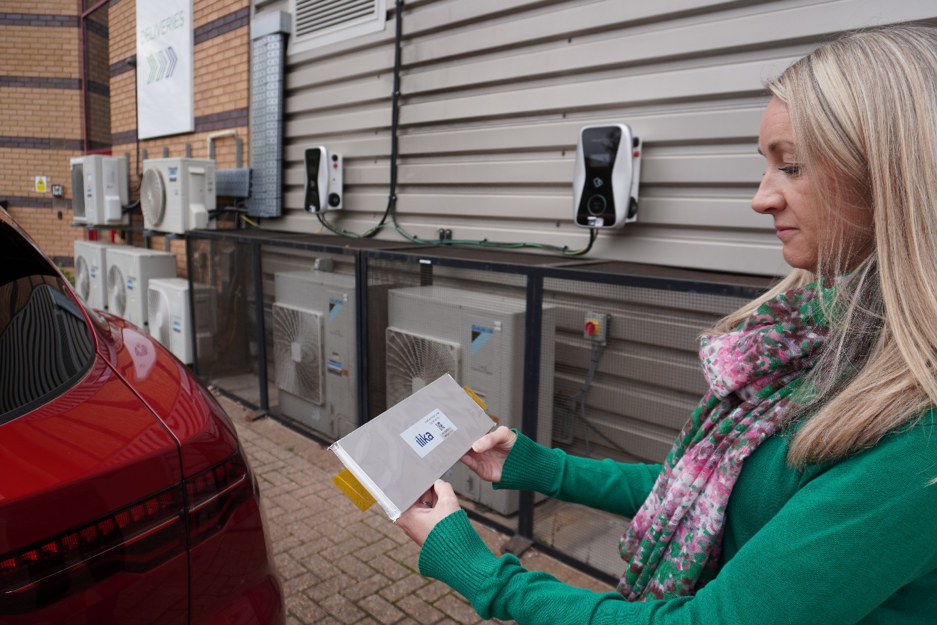
In 2019, we moved to larger facilities in order to kick-start this new “Goliath” R&D program, although still local to Southampton, UK. The team increased in size (we are now about 70 employees) and a culture-change, already initiated with the Stereax program, needed to happen: whilst Ilika will always rely on its pool of world-class researchers and scientists with academic backgrounds, the team needed to be re-enforced with colleagues with industrial experience. A new generation of Ilika employees with engineering and manufacturing background joined us, led by industry veterans who knew how to turn ideas into commercial products (Robin Bell, NPI Director), who had experience building facilities from R&D to gigafactories (Brendan McCarthy, ex-BMW and UK Battery Industrialisation Centre, UKBIC) and could interact with authority with our supply chain (Simon Brimble, ex-Delphi).
The Goliath program will follow the same business model as Stereax. Whilst following a road map of new products and increasing their Technical Readiness Levels (TRL), we are in parallel increasing our Manufacturing Readiness Levels (MRL) by collaborating with tool vendors, supply chain and scale-up facilities like UKBIC. We are already acquiring low volume, production-representative tools and commissioning them in our Goliath pilot facility. We continue to work closely with automotive industry partners, with recent collaborations including input from BMW Group, WAE and Agratas. By proving that our chemistry fulfils battery cell safety and performance needs from the automotive industry and exemplifying manufacturing on relevant equipment, Ilika aims to eventually license the Goliath technology out, in the same way that we did with Stereax.
The Next 20 Years
By mixing long term plans with timely pivots, Ilika has created solid foundations for future growth, uniqueness and innovation. Of course, nothing could have happened without the Ilika colleagues, who worked hard to make Ilika what it is now. On 15th May, our anniversary day, we raised a glass and cut a large cake with 20 candles… and then went back to work for 20 more years of cutting-edge research, product development and commercialisation.