HISTORY in the making
Posted on: in Blog
“Consortium of UK companies, universities and one government catapult join forces to develop a very British solid state battery for electric vehicles”. This was the kind of headlines you could read 12 months ago, at the start of the HISTORY collaboration program, funded by Faraday Battery Challenge (FBC). This blog aims to keep you informed of the program’s progress.
Led by Ilika, HISTORY essentially develops in 2 years Ilika’s first prototype cell for EVs, the “Goliath” cell, using Nexeon’s silicon anode material, with electrodes formulated by CPI, and with modelling and characterization from the University of St Andrews, University College London and Imperial College London. In addition, HSSMI is reporting on Life Cycle Analysis and End of Life of the cell.
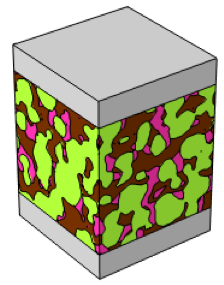
3D model of a Goliath cathode based on CT experiments information (Imperial College)
First, and rather importantly, I am happy to announce that the consortium passed the mid-point review from FBC with flying colours and will carry on working full steam ahead to reach their goals! FBC wanted to hear about the program’s technical progress and commercial exploitation opportunities: they appeared to be satisfied with our responses and the support provided by steering committee members BMW Group and WAE.
The consortium has actually grown since the program started: Prof. Paul Shearing, formerly of UCL, joined the University of Oxford last year, adding yet another prestigious name to the team!
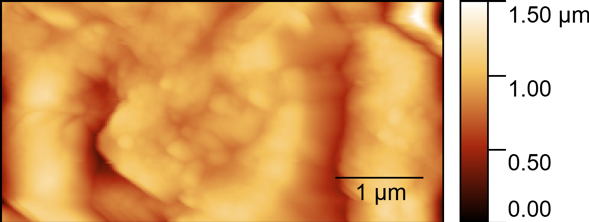
AFM data provided by UCL
Now work is, as we say, in progress, but I can update you on the key activities and achievements from Year 1. To simplify my summary, I will discuss one Work Package (WP) at a time. WP1 is the admin work package, nothing exciting here. WP2, led by Ilika, focuses on the development of the cell itself, towards its final specs. Two significant achievements were made public at the end of 2023 regarding Ilika’s progress, see Two Major Milestones Reached for Goliath Solid State Cells for Electric Vehicles.
In WP3, University of St Andrews used Raman Spectroscopy to study the interaction between electrode and solid electrolyte materials during the cell manufacturing process: this is key to delivering a high-performance cell. They also confirmed, using x-ray Diffraction and Scanning Electron Microscopy, that there should be no concern about the stability during storage and handling of the chemicals used in the manufacture of the “Goliath” cell, in environments typical of lithium-ion battery manufacturing.
WP4 is led by Si anode material manufacturer Nexeon. They produced a range of Si-containing composite anode electrode components with binder and conductive additives which were incorporated in the “Goliath” cell. With very exciting early results, the remaining work now consists of identifying through testing which of Nexeon’s Si-based anode electrode formulations provide the optimal cell performance.
CPI, who lead WP5, are very much the link between Ilika and Nexeon, whereby they developed and tested various scaled anode electrode formulations utilising Nexeon’s Si-based anode material, and delivered coated electrodes to Ilika for insertion in the “Goliath” cell. In Year 2, CPI will essentially transfer the technology they have developed to Ilika, who will take it forward to pilot production.
In WP6, UCL used their world-leading Atomic Force Microscopy (AFM) and X-ray CT scanning techniques to charaterise the components of the cells at the particle level. This is very important because it will improve the understanding of potential failure mechanisms during the operation of the cell (such as fracturing or delamination) and eliminate these as much as possible. UCL’s equipment has also provided key data to WP8 (the Modelling WP) through mapping of mechanical properties across the electrodes. In Year 2, UCL, with new partner University of Oxford, will use optical scanning techniques to further analyse failure mode, by comparing cells at the beginning and end of life.
WP7, also led by Ilika, is the Test Plan work package. Here, the team has designed a set of experiments and tests intended to understand in detail how the “Goliath” cell will perform. HALT was first, i.e. Highly Accelerated Life Testing: essentially a set of tough tests intended to take the cell beyond its limit, and ideally destroy it, to understand what its limitations are. Then comes performance and safety tests. Performance tests are really looking to understand how fast you can charge the cell, how many times you can charge and discharge it, how much power and energy it contains etc… But of course, performance is only one half of the “Goliath” cell’s USP (Unique Selling Point). High safety is the great differentiator between SSB and Li-ion, this is why an extended panoply of safety-related tests will take place (crushing the cell, nail penetration, thermal runaway tests…).
Imperial College is leading WP8, which, as mentioned above, aims to create an electro-chemo-mechanical model of the cell: this is a key deliverable. Creating a computer model of the cell is ideal for understanding the correlation between physical parameters such as particle size or loading conditions and cell performance. UCL developed a multiscale (micro/macro) framework which helps connect material characteristics to battery specs. Essentially, this is a tool to understand how to design the optimal cell.
Last, but not least, HSSMI are leading WP9: circular economy and sustainability are important to all the partners, and HSSMI are experts at evaluating this for new technologies. For the first time, they are modelling the carbon dioxide, minerals depletion and water pollution related to the materials in Ilika’s SSB, its manufacture, and finally usage, comparing it with the environmental impact of lithium-ion batteries. In Year 2, End of Life and recycling processes will be explored.
Hopefully, this short summary will give you an appetite for following this essential piece of work, and be sure that I will update you soon with further information!
Denis Pasero