BUS100 – Collaborative Project Between Ilika and UKBIC Comes to an End with Positive Findings
Posted on: in Blog
In May 2022, we began an Advanced Propulsion Centre (APC) funded collaborative project with the national battery manufacturing development facility, the UK Battery Industrialisation Centre (UKBIC). The objective of the project, named BUS100, was to determine if a MWh-level manufacturing line for Ilika’s Goliath solid state batteries (SSB) could, in principle, be installed economically at UKBIC, utilising some of the existing lithium-ion battery manufacturing (LIB) equipment in order to supply automotive cells to Ilika’s customers at an acceptable price point. Demonstrating cell manufacturing on production-intent equipment, at MWh-scale, is key to Ilika’s scale up plans. This would de-risk future mass-production of its SSB cells at GWh-level and enable adoption by an automotive OEM’s platform.
The project was a follow-up from the SOLSTICE collaborative project we carried out with Comau which concluded that 70% of existing LIB equipment can be re-used for SSB manufacture. Whilst SOLSTICE was a theoretical exercise, BUS100 aimed to confirm SOLSTICE findings by working with a company that produces LIB at exactly the right throughput for Ilika’s next scale-up step. Both projects are part of Ilika’s strategic industrialisation plan which aims to have A-samples produced at our headquarters in Romsey, UK, after a first scale-up exercise to reach 1.5 MWh/yr (Ilika’s current cell development facility) for automotive OEM validation. This will be followed by production and delivery of B-samples which could be carried in a mid-scale facility, using production-intent equipment and processes, demonstrating that Ilika’s SSB can be manufactured at high volume.
Now completed, the BUS100 project found that, subject to trials and acquiring additional equipment, it would be technically possible to utilise part of the existing UKBIC electrode line to manufacture our SSB cells. Using some of UKBIC’s industrial scale equipment for a large scale trial, albeit for a smaller part of the year only, could provide sufficient cells to our customers, and demonstrate production at scales relevant to gigafactories.
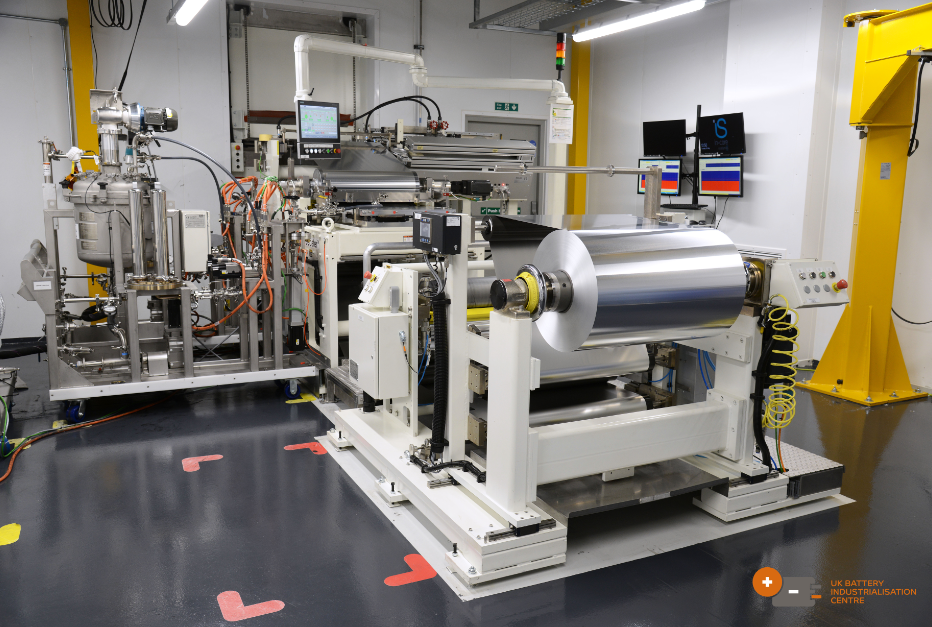
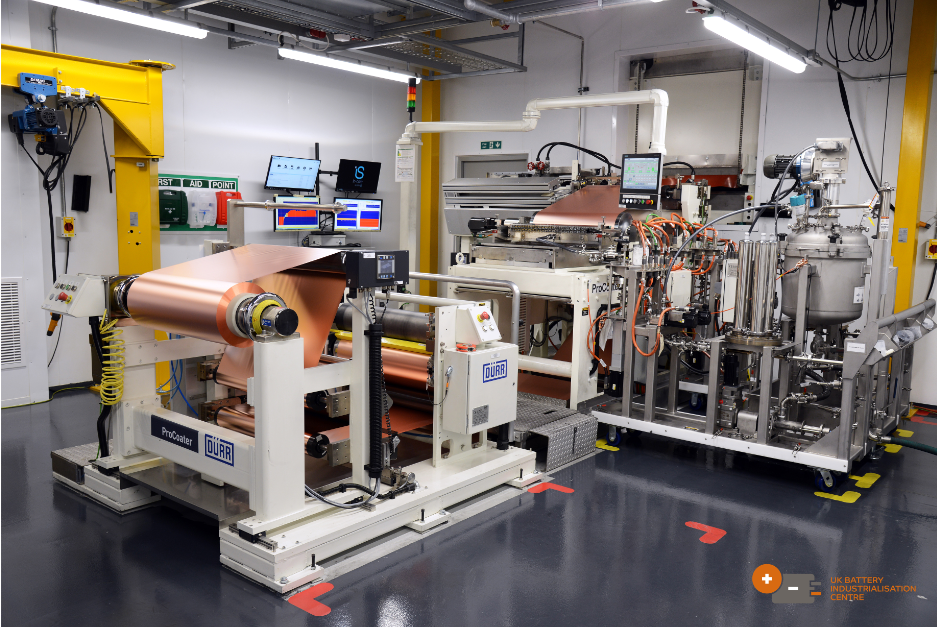
BUS100 project structure and work package descriptions
The first half of the project was primarily a knowledge transfer of Ilika’s processes to the UKBIC team. This resulted in a gap analysis of those processes Ilika needs versus those that UKBIC already have in place. It also demonstrated that UKBIC’s existing specialist equipment could be utilised for Ilika’s processes in all necessary areas including electrode manufacture, formation, ageing and testing.
The second part focussed on determining the cost of installing the line at UKBIC which was split into 3 work packages. One work package focused on operations and included:
- the creation of a line layout, taking into account currently available and future space at UKBIC, including dry and clean rooms for relevant part of the process;
- a throughput analysis ;
- a study of the utilities and services required, including electricity, water, compressed air, gases, fire detection and suppression;
- the off-line quality systems and in-line process inspections were finally mapped onto the line layout.
Another work package focused on Health, Safety, and Environmental Assessment for installing a solid state battery line at UKBIC and included:
- an assessment of the compatibility of SSB’s chemistry with UKBIC’s carbon bed and condenser equipment;
- outbound logistics storage of live batteries and safety compliance;
- a comparison between the recycling and disposal procedures of LIB and SSB;
- a process for risk avoidance for materials used in Goliath, not currently used at UKBIC.
The final work package created a cost assessment of the potential scale-up, including training requirements and site assessment procedures. The financial analysis included rental space, use of UKBIC electrode rolls, utilities and services as well as other CAPEX costs, for example Formation, Ageing and Testing equipment.
Once all these were completed, the BUS100 findings were included in an Economic Feasibility Report which will enable Ilika to make a business decision on the next step for scaling up our Goliath solid state batteries.
Whilst detailed findings of the project remain confidential, we can confirm that:
- UKBIC’s anode and cathode electrode production line could be used for Ilika’s purposes of manufacturing SSB for part of the year subject to trials;
- A purpose-built assembly line would be required to be constructed within the facility for the solid-state battery’s unique manufacturing process;
- The scale up project was fully costed and Ilika calculated the price point for this level of throughput.
Overall the collaboration has worked very well with learning on both sides. We hope to continue with the relationship.
Jeff Pratt, UKBIC’s Managing Director, said: “We are pleased with the outcome of this comprehensive feasibility study, which supports Ilika’s ambitious plans for an advanced solid state pilot line being developed and established in the UK. The collaborative work between Ilika and UKBIC has synchronised vital knowledge and factual data for scaling up future generations of battery technologies towards volume production.
“Solid state technology is an exciting proposition for high performance batteries. It is this potential that cannot be ignored. The proposed development of a state-of-the-art solid-state pilot line would be vital for the UK’s long-term ambitions as a battery superpower.”
Next steps will be important for Ilika, as we will aim to evidence the conclusions drawn in the BUS100 project with large scale trials. Follow up work is already taking place in project STEP which deals with trialling equipment not available at UKBIC, with UK vendors. A pilot automated assembly and stacking line is also in planning in our Romsey facility. Once built, the OEM developing this line would then be in a position to create a larger version, creating a balanced output assembly line.